News
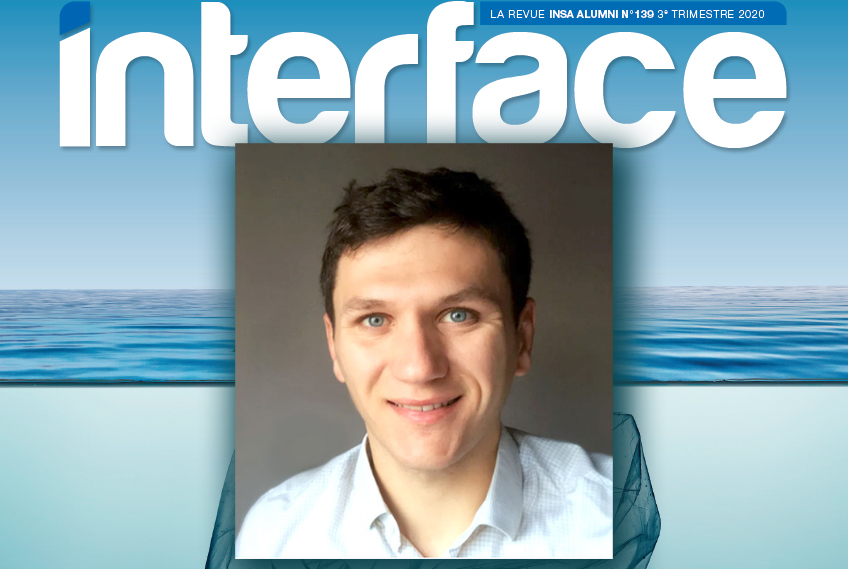
Paul FLURIN (LY-GMPP-2015), Co-fondateur de TIZU
POURQUOI EST-CE SI DIFFICILE DE RECYCLER LE PLASTIQUE ?
Sous le feu des projecteurs depuis de nombreuses années, le recyclage des plastiques est à la peine. Manque de volonté ou réelles difficultés techniques ?
A première vue, ça n’a pas l’air si compliqué
Le recyclage d’un thermoplastique peut être simplissime. Sa capacité à fondre nous permet de récupérer un déchet pour le changer de forme et en faire un nouveau produit. En boucle fermée, le recyclage des déchets de production simple est d’ailleurs très répandu, car très efficace. On broie les pièces rebutées, on s’assure que le broyat n’a pas été contaminé et on remet le tout dans la machine pour faire de nouvelle pièce : facile. En cycle fermé, le polypropylène peut ainsi être recyclé plus de vingt fois avant de commencer à perdre ses propriétés. Les conditions sont les suivantes :
- Pièce mono-matière
- Flux de déchets mono-produit
Par exemple, les bouchons de bouteilles en plastiques répondent à ces critères (à la couleur près), et de fait, ils sont recyclés depuis longtemps !
En France, ce recyclage en boucle fermée est présent depuis les débuts de la plasturgie. Souvent même internalisé dans les sites de production. Cependant la conjonction de ces deux conditions est très rare, si bien qu’on estime que seul 6% de la production de plastique est recyclée à l’échelle nationale (26% pour les emballages).
Les mille visages du plastique : l’infini des possibles
La fabrication des pièces en plastiques est le résultat du travail de toute une filière, depuis le raffinage des matières premières – principalement des naphtas pétroliers – jusqu’à leur mise en
forme par les plasturgistes. Des vapocraqueurs[1] aux injecteurs ou autres thermoformeurs[2], en passant par les formulateurs et les compoundeurs[3], chaque corps de métier influe sur les propriétés physico-chimiques du matériau, permettant une infinité de possibilités pour les concepteurs de pièces plastiques.
En faisant varier la taille, la composition et la ramification des chaînes macromoléculaires, on contrôle finement les propriétés mécaniques, physiques, thermiques et même électriques des matières plastiques. En leur ajoutant des additifs, on maîtrise leur couleur, leur coût, leur transformabilité. Enfin en combinant les plastiques au sein d’une même pièce on évite les compromis et on se rend capable de répondre à des cahiers des charges d’une complexité exceptionnelle !
Un concepteur a accès à plus de soixante mille références commerciales de plastique suffisamment connues pour être référencées sur des sites comme Campus Plastics ou UL Prospector. Il a en plus la possibilité de les associer au sein d’une même pièce. Des possibilités infinies !
Conflit d’intérêt
Cet infini des possibles s’accommode très mal de l’idée du recyclage. En effet, les déchets plastiques, une fois séparés du reste des déchets, doivent être séparés par résine. On parle souvent de 7 types de résines, mais pour atteindre une qualité « matière vierge », il faudrait une filière pour chaque référence commerciale de plastique, soit une quasi-infinité !
On se retrouve à devoir sortir du recyclage en boucle fermée pour la majorité des plastiques. Et ça génère une cascade de problèmes.
Quand les plastiques ne sont pas mélangés dans un même produit, les flux de plastiques se retrouvent mélangés par les circuits de traitement de déchets (collecte, absence de process dans les usines). Parfois même, certains flux sont mono-produit et mono-matière, mais tellement petits qu’on les mélange à d’autres, car leur trouver preneur serait trop long pour trop peu de résultat. Il faut ajouter à cela que la traçabilité des déchets est souvent impossible, et qu’une pièce en plastique a une composition chimique complexe. On doit alors vérifier l’innocuité du matériau.
Aussi, caractériser complétement un plastique en laboratoire peut coûter plusieurs milliers d’euros. Une pièce plastique de nature inconnue dans un flux de déchets ne pesant souvent que quelques grammes, la tâche devient herculéenne. Les machines de tri ne seront jamais à la hauteur de ce défi colossal sans une réorganisation des phases de conception.
Le contexte économique est en plus désastreux pour le recyclage. Avec des cours du pétrole historiquement bas, les plastiques de commodités se sont durablement installés à moins d’un euro du kilo. Cela laisse très peu de marge de manœuvre pour la collecte, le traitement et la remise sur le marché des déchets plastiques. Seul le PET[1] des bouteilles s’en sort, grâce à une pression des consommateurs qui conduit les industriels à acheter de la matière recyclée, bien que près de 50% plus cher que la vierge.
Chez TRIVEO, entreprise de l’Economie Sociale Solidaire de la Plastics Vallée, on fait le pari que ce tri en une infinité de flux sera la clé d’un recyclage de qualité, et que le tri manuel est le meilleur moyen d’y arriver ! Mais la concurrence du pétrole pas cher fait souffrir la petite entreprise et l’oblige à se cantonner pour l’instant à des flux intermédiaires, trop complexes pour le recyclage conventionnel mais suffisamment simples pour être rentables.
L’éco-conception, une démarche pas encore intégrée
L’éco-conception peut être salutaire, mais cette démarche n’a rien d’une promenade de santé. Produire une pièce en plastique s’apparente à un petit miracle économique. Prenons l’exemple d’un pare-chocs automobile. Le cahier des charges regorge de contraintes très difficiles à concilier. En plus d’assurer la sécurité du véhicule, cette pièce complexe doit s’intégrer dans l’esthétique de la voiture, être la plus légère possible, tout en embarquant une bardée de capteurs. Elle doit être
rapide à assembler, et intégrer des tolérances dimensionnelles très fines et bien-sûr coûter le moins cher possible. Enfin le développement de ces pièces étant confidentiel, la possibilité de leur recyclage n’est évoquée avec les recycleurs et/ou éco-organismes qu’une fois la production lancée et rôdée. Les coûts d’investissement pharaoniques et la complexité du développement rendant tout changement postérieur très coûteux, la recyclabilité et/ou l’intégration de matières plastiques recyclées arrivent comme un cheveu sur la soupe.
J’ai souvent entendu des questions du type : « Mais on ne peut pas valoriser mes pièces dans des produits moins nobles, comme des palettes ? » La réponse est non. Il n’existe pas vraiment de produits « poubelle » qui absorberaient les déchets plastiques produits chaque année dans le monde. Et quand bien même, les quantités astronomiques de déchets cherchant repreneurs impliqueraient que le producteur de déchet paie cher pour fournir son plastique, par pur mécanisme de l’offre et de la demande. Avec un coût d’enfouissement autour de 150€/tonne, le choix de l’économie linéaire est vite fait pour les producteurs de déchets.
La question du recyclage, pour être traitée efficacement, doit s’inviter dès le début du développement des pièces. C’est le défi de l’éco-conception. Si elle se généralise, elle sera un virage majeur dans la plasturgie. Car les pièces plastiques tendent depuis de nombreuses années vers la complexification à outrance.
C’est un changement structurel car cela implique pour les metteurs sur marché de faire des concessions sur les performances, notamment esthétiques, mécaniques, et économiques des produits en plastiques, et cela implique de perdre un avantage concurrentiel. La démarche n’est donc acceptable que si elle s’impose à tout le monde.
C’est l’argument phare des plasturgistes européens, prêts à accompagner des règlementations européennes contraignantes, mais seulement si le contrôle des importations permet de leur éviter une concurrence déloyale.
Les ingénieurs ont le pouvoir de changer les choses
Tout comme pour l’efficacité énergétique, la réparabilité ou la réutilisation, tous les ingénieurs peuvent pousser pour faire de la place aux matières premières recyclées dans leurs conceptions. Les phases les plus amonts des projets offrent la possibilité de s’imposer des contraintes environnementales plus fortes. Même si ces choix stratégiques sont le théâtre de rapport de forces entre acteurs industriels, les ingénieurs ont plus de pouvoir qu’ils ne le pensent !
Paul FLURIN (LY-GMPP-2015),
Co-fondateur de TIZU, marque de mobilier upcyclé[1], et consultant en recyclage des matières plastiques.
L’upcycling, est un procédé qui consiste à réintroduire dans un cycle de création des matériaux ou objets qui n’ont a priori plus d’utilité. Ils peuvent être détournés pour devenir tout autre chose, dans le but de générer le moins de déchet possible.
Le vapocraquage est un procédé pétrochimique qui consiste à obtenir, à partir d'une coupe pétrolière telle que le naphta, ou d'alcanes légers, des alcènes (éthylène, propylène) mieux valorisés.
Thermoformage : technique de mise en forme de certains matériaux sous l'effet de la chaleur et d'une contrainte mécanique.
Société spécialisée dans la fabrication de composanst, tels que : thermoplastique rubber (TPR/TR) base SBS (de type Kraton D), thermoplastique élastomère (TPE) base SEBS, SEEPS (de type Kraton G), thermoplastique oléfine (TPO), des thermoplastiques à charge minérale (talc, carbonate de calcium [caco3]), thermoplastiques renforcés avec de la fibre de verre, mica, ou encore des compounds spéciaux avec du graphite, sulfate baryum et autres.
Polymère de type polyester saturé, par opposition aux polyesters thermodurcissables. Ce polymère est obtenu par la polycondensation de l'acide téréphtalique avec l'éthylène glycol.
Aucun commentaire
Vous devez être connecté pour laisser un commentaire. Connectez-vous.